Want to Reduce Costs? Start by Avoiding Rework in the Field
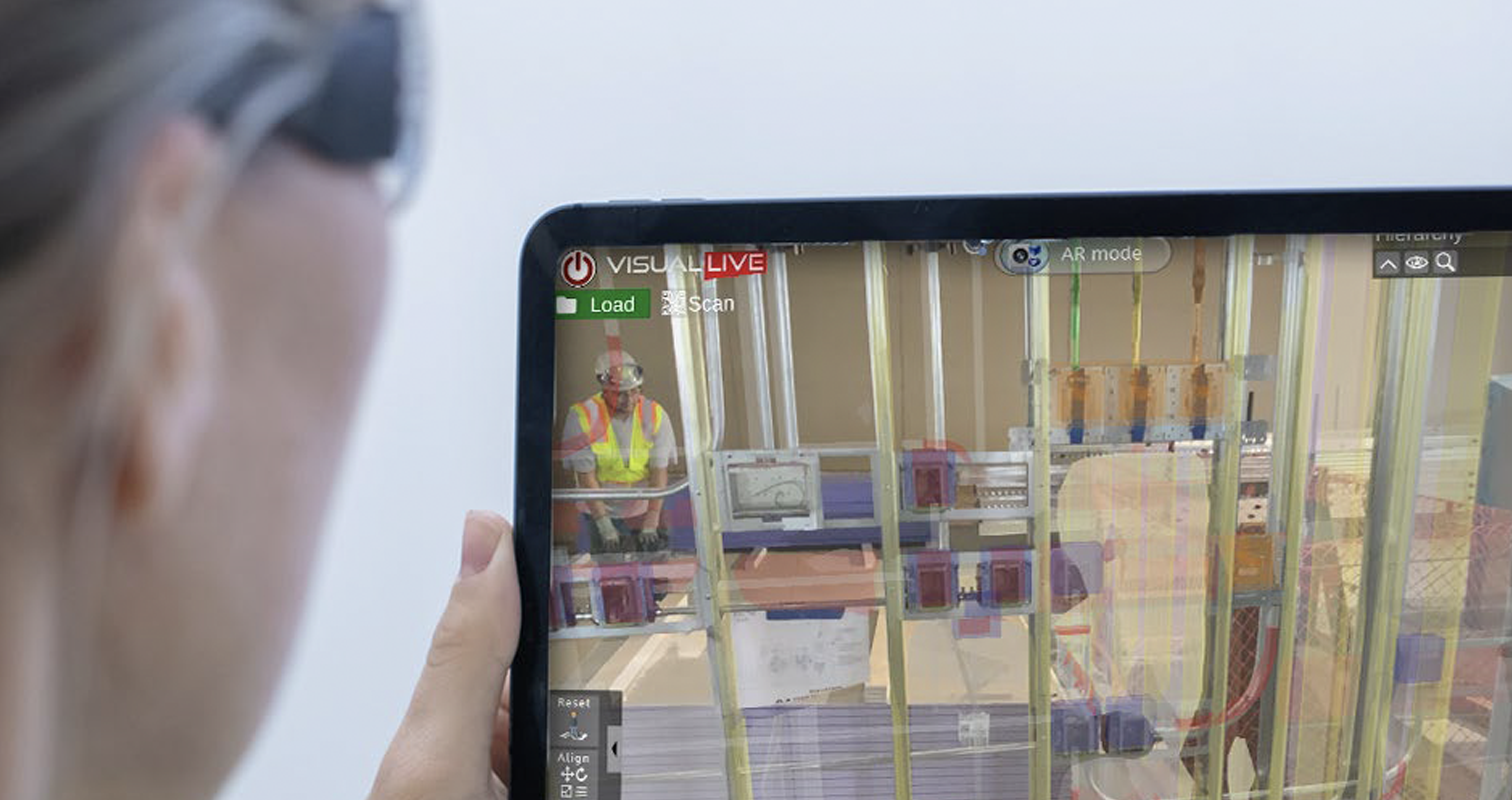
Construction rework costs money. It eats up valuable time that you and your team don’t have. It leads to low morale and frustrated clients. So why does the industry continue to struggle with it?
MCSER (the Mediterranean Center of Social and Educational Research) reveals that approximately 30% of the work done by construction companies today is rework. It’s been a long-accepted view that rework is just part of the job. But imagine the productivity and profitability gains you could experience if you brought that percentage down—even a little!
As Dave McCool, product manager at Procore Technologies, points out, the benefits of reducing rework go far beyond money and time. “Studies show that around 60% of injuries are caused by rework and the shortcuts involved when there’s a push to meet an owner’s deadline. All it takes is one time where you try to do things differently to save hours.”
30% of the work done by construction companies today is rework
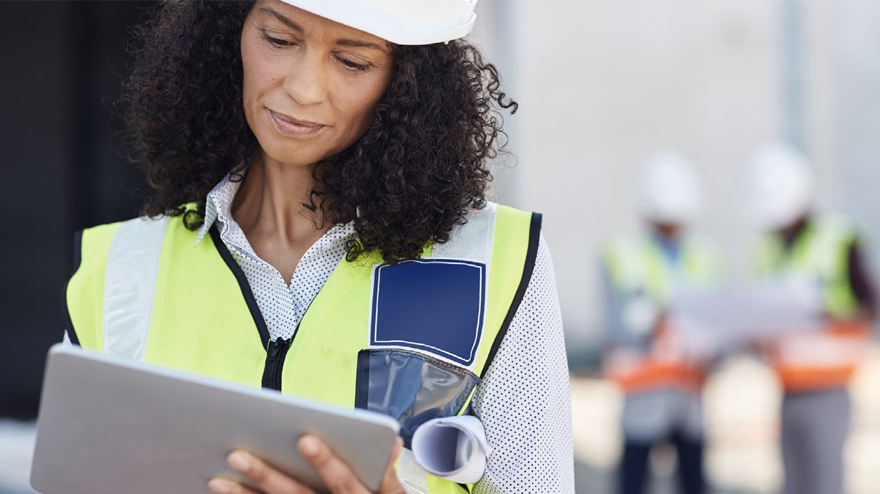
Where does rework come from?
Rework will always be part of construction; it will never completely disappear. But you can take steps to rein it in when you understand where rework comes from and what causes it.
As Apollo Mechanical Contractors’ Senior Project Manager Eldon Parry points out, some rework is out of your control, such as last-minute client requests or logistical changes (like using a slightly different material due to shipping delays). Other causes can be linked to human error, such as mismeasuring or selecting the sheet metal gauge for the job.
No matter what form it takes, the opportunity for rework arises the very moment a project starts. When work must be redone, it can often be traced back to:
- Poor communication and transfer of final decisions — especially during the shift from pre-construction to construction
- Not involving trade partners early enough to coordinate design and ensure constructible details
- Not coordinating design with existing site conditions
- Not confirming details in repetitive spaces, such as hospital or hotel rooms, where a design will be replicated
- Lack of pre-installation meetings to discuss specifications
- Poor document control
- Increases in overtime, which can lead to more mistakes
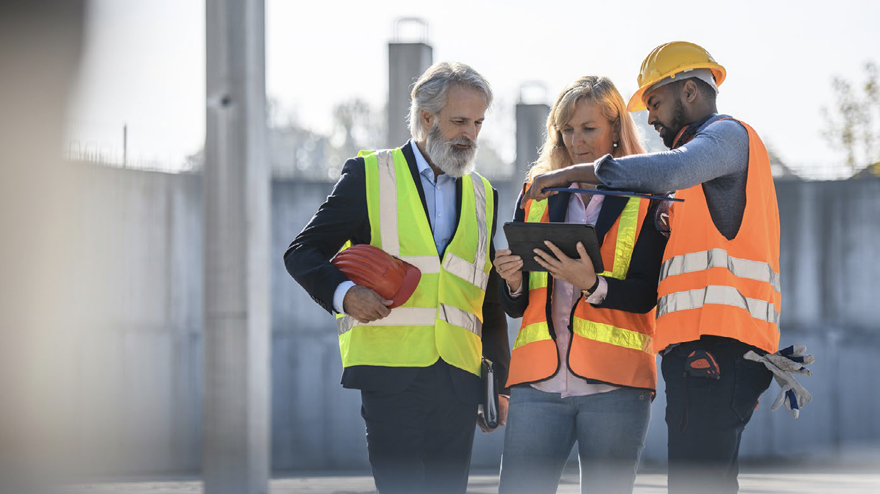
Dustin Ridley, senior VDC manager at DPR Construction, says his team has learned to keep a close watch on “unseen areas” during project coordination. When they create VDC execution plans, they ask trade partners to model certain levels of information. In some cases, however, creating these models isn’t possible.
For example, DPR Construction may ask electricians to create models for large feeders and large runs of branch conduit. But when workers get to the field and begin installation, they sometimes find that the smaller conduits not in the model (the “unseen areas”) start to add up (such as conduit containing circuitry that runs from fixture to fixture). If workers aren’t paying attention or checking against the coordinated model, then conduit may be installed through zones that were supposed to remain clear.
“A lot of this can be prevented with good design coordination, field investigation through laser scanning, and communication with the design team so they can design to existing conditions,” says Ridley. “If you can get to a point where you can kick out a coordinated product, you’re going to have fewer issues in the field.”

The impacts of rework: Real-world examples
Almost every contractor has a story to tell about rework: a project that completely missed the mark because so much work had to be redone.
For example, Parry recalls a project where pipe had to be replaced because the wrong type was installed; the spec called for a certain model from a specific manufacturer. This mistake resulted in nearly $300,000 of rework on a $1.2 million job.
“We’ve also had scenarios where pipe actually went in the wrong way,” says Parry. “We were supposed to go right instead of left, for instance. The detailer thought he was interpreting something correctly, but he was not.” In one case, Parry says that mistake led to nearly 100 linear feet of rip-and-replace work that had to be redone.
“A lot of knowledge is missed because someone doesn’t understand what you’re saying or what’s being presented to them,” Parry explains. “Therefore, they don’t know how to ask the right questions—or if they should even ask a question at all.”
For McCool, costs of rework have far surpassed the impacts of lost time and money. While he was working for a construction company in California, everyone was under pressure to adhere to a very tight deadline. Shortcuts were made in an effort to stay on track, and a foreman nearly lost his life due to rework being done too quickly and carelessly. His foreman survived but is living the rest of his life in a wheelchair. “That drives home the need to fix this problem,” he says.

Where to start when addressing rework
Before you seek out technology to solve rework problems, there are some simple steps you can take to prepare a solid foundation.
Ridley says that owner alignment is one of the first steps his team takes. They start by identifying distinguishing features of work (DFOWs) on each project. “We talk to owners about what’s in the wall, on the wall, on the floor, in the floor, on the ceiling, and above the ceiling in each room because all these things interact with each other,” he explains. “We ask the owner, ‘Do you actually want this picture frame here? If you do, do you understand how it will interfere with the way the door closes and where the receptacle is located? These small details turn into rework in the field if they’re not clarified upfront.”

McCool likes to take that a step further by having pre-installation meetings to go over everyone’s roles and, in high-risk projects that involve lots of repetition, also look at physical mock-ups. “That’s so valuable to get owner feedback,” he explains. “Then everyone knows everything is exactly how it’s supposed to be.”
Validating work is another worthwhile step. A double- or triplecheck always helps, but it also takes time. The more complex the project, the more hours you’ll spend validating.
“No one has weeks to validate things like measurements. You rarely have a day to spare,” says Parry. “The best thing you can do is spot check. We used to have someone go out and pull tape measures to check tight spots and areas we thought were bottlenecks. Sometimes, what we thought would be trouble areas weren’t. Other spots turned out to be challenging instead. It can be a guessing game.”


Integrating technology: How augmented reality decreases rework
Once fundamentals are in place, the next big opportunity to reduce rework comes with augmented reality (AR). Even if you’re not ready to use the technology now, AR is something you won’t be able to ignore for long.
AR is being used in many industries—from education and automotive to construction and aerospace—to improve efficiency. In a recent study, Boeing rolled out its own AR program for wiring diagrams and decided to measure ROI.
According to Boeing Research & Technology Associate Technical Fellow Paul Davies, AR has shown a 90% improvement in first-time quality when compared to 2D information on an airplane, along with a 30% reduction in time spent on wiring jobs. Those are huge jumps in quality and productivity.
90% improvement in first-time quality with AR when compared to 2D information
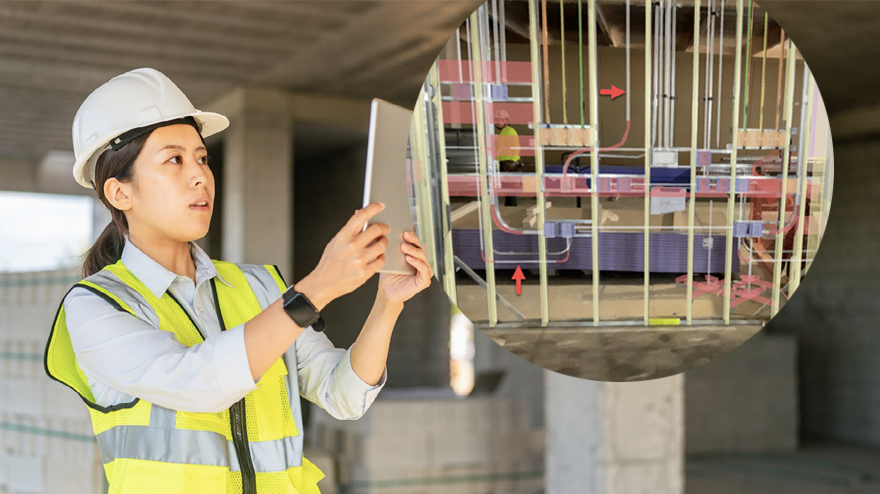
Deciding how to use AR often comes down to communicating with the project team to find out what everyone needs, says Ridley. Right now, his team is using it on a 650,000-square-foot healthcare project involving in-wall coordination. When the team heads to the field, they use AR to focus on one room at a time, referring to the model to make sure systems and devices are installed in the right place.
“When we overlaid the very first room with augmented reality, we could see that every device was where it needed to be,” says Ridley. “We also recognized an extra device in the room that wasn’t in the model, which led to a discussion about where it came from. It turned out to be a thermostat that made its way to the field but not to the coordination model. When you’re able to overlay the coordinated room with field conditions, you open up new levels of discussion.”
McCool says one of AR’s best uses is to track jobsite productivity. “You can compare the field to the model and find out what’s been installed since you were last there. If you notice you’re missing half the devices that were supposed to be installed in the ceiling by that point, you can check and see what’s going on. You instantly know whether you’re on schedule.”

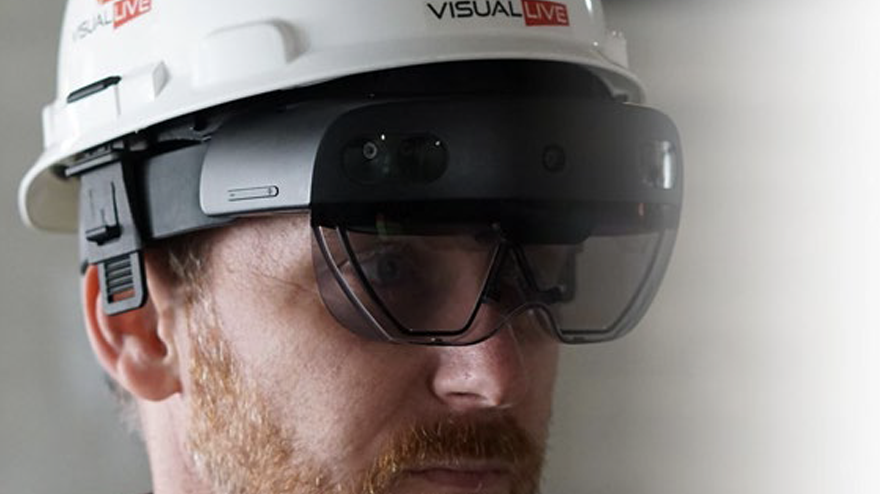
For Apollo Mechanical Contractors, AR has been a game-changer. Because the company doesn’t have in-house programmers, it needed an out-of-the-box solution designed for construction.
“What drove us to use the technology was rework,” says Parry. “Detailing is at the forefront of what we do. If our detailers don’t produce quality work, then our jobs struggle to make money and we deal with rework all over the place. We have to be faster and better than the next guy, and this helps us do that. Rework is one of the biggest differentiators between a profitable and unprofitable project.”
He even credits AR with saving valuable time and expenses on a recent auto plant project. An Apollo team was changing out and augmenting a system to feed a new section of the factory. They had to get lines up and running within a single day to avoid impacting the plant’s revenue. To make sure things went smoothly and avoid rework, the team took AR to the site to review everything beforehand.
During the process, the team caught mistakes they were able to fix before the shutdown. “Had we not done that, some of the fabrication would have come out incorrectly. To still get the work done in one day, we would’ve had to throw many more bodies at it,” explains Parry.


He has also seen AR reduce rework by maximizing employee potential. He notices improvements in worker confidence: They know the data is accurate, can access the information they need, get to see things in place before they’re installed, and provide input on system routing.
While rolling out new technology can be stressful, being able to immediately see how AR makes life easier puts field workers’ minds at ease and boosts productivity. “When they see things fitting better, they get excited because they know they won’t have to deal with rework,” explains Parry. “They get a lot more done in a day and get praised for it, so they go home proud.”
It has also opened up Apollo’s talent pool. Finding talented workers who can conceptualize and apply mathematics to fit systems into a space was tough—but relying on AR to visualize and verify design work allows the company to hire laborers with fewer years of experience.
He believes AR holds great promise for the future of construction—especially as younger workers join the field and need to be trained quickly. Having this tool to boost trust and decision-making can make sure systems are installed correctly the first time, reducing rework while keeping projects on track and on budget.
Learn how you can build and deliver custom real-time 3D experiences for AR, VR, mobile, desktop, and web.
studioID by Industry Dive
studioID is Industry Dive’s global content studio offering brands an ROI rich tool kit: Deep industry expertise, first-party audience insights, an editorial approach to brand storytelling, and targeted distribution capabilities. Our trusted in-house content marketers help brands power insights-fueled content programs that nurture prospects and customers from discovery through to purchase, connecting brand to demand.
Get the e-book
Fill out this form to access cutting-edge insights and solutions from industry experts