Enhancing the Workplace with XR, VR, and AI Tools

Across industries, extended reality (XR) developers are building bespoke applications to improve the way teams communicate, iterate, and upskill.
What’s motivating the workplace XR trend?
- XR provides new ways for cross-discipline teams to interface with data and collaborate
- Virtualization accelerates design iteration and permits simulated tests with greater control
- XR overcomes pain points such as limited contextual depth or physical relocation
- Democratizing access to siloed 3D data can add value to existing and often costly data
- Training can be performed in risk-free environments with native metrics for analysis
The increasing affordability of creating 3D data is a key factor behind this push. As technical advancements, including multispectral cameras (for truer color indices) and LiDAR emitters (for accurately measuring distance), come to consumer-grade hardware and mobile devices, enterprises can cheaply and efficiently design digital versions of real-world locales, products, and systems in order to jumpstart the development of practical XR applications.
In most cases, these custom applications address emergent business needs such as cost reduction or improving operational efficiency. By providing a common visual language for interdisciplinary teams, workplace XR applications allow organizations to derive additional value from the kinds of costly 3D data already in use, for example, in factory production, architectural prospectus, or internal research and design.
When organizations embrace data transparency and enable XR developers to access and manipulate this data in real-time 3D frameworks, they soon realize the actual value of that data lies in its ability to synergize human effort without requiring technical expertise or expensive licenses to open proprietary data formats.
With the global XR market eyeing a $1.9 trillion (USD) valuation, XR augmented work has the potential to revolutionize the professional landscape. XR applications built using real-time 3D technology will soon augment human effort in a workplace renaissance akin to the advent of personal computing or the widespread adoption of cloud infrastructure. This isn’t a far-flung future – it’s already happening today.
In this e-book, we’ll encounter XR developers who have paired 3D data with 3D development frameworks to build immersive simulations and XR tools. When deployed to commercial spatial-computing platforms and mobile devices, these applications enrich their team’s insights and offer new, more meaningful trajectories of collaboration.
Use cases for XR apps
Before diving in, it’s important to contextualize our study of these innovative development teams. What made them choose to invest in XR? A few broadly defined use cases emerge:
Collaboration
Certain XR teams create real-time 3D applications to present product design demonstrations or create a means to conduct remote facility inspections with a digital twin. Other specialized XR tools offer instant visual insights to help field technicians coordinate with team leads in real time across distances. Though the implementation may change, these kinds of solutions solve the problem of geospatial coordination and enable deeper presentation contexts via dynamic perspectives.
Simulation
The benefits of simulating real-world settings can’t be overstated. From virtualized industrial machines to global shipping trackers, 3D simulations are a powerful complement to design iteration, stress testing, and triage – especially when backed by real-time data. These solutions are especially useful for optimizing existing processes and analyzing systems that incorporate many interdependent components.
Education
Now that virtual reality headsets have become more affordable, many enterprises are deploying VR training modules that offer low-stress, risk-free environments for learning complex processes. Depending on the implementation, VR training can improve retention with repeatable lessons, save module states for individually paced learning, and ensure uniform proficiency standards with built-in metrics tracking and assessment.
Innovation
Beyond the intended use cases listed above, the innovators we’ll meet in this e-book have found new ways to repurpose and reinterpret existing 3D data that translate to cascading benefits across their organizations, including wholly novel use cases.
XR applications can generate potentially game-changing ROI in terms of explicit cost savings, increased situational awareness, and swifter team collaboration. It’s time to meet the innovators who use Unity’s real-time 3D development platform to actualize these and other, often unanticipated benefits.
Industry Closeup: Automotive OEM

Innovator: Volvo Cars
- Use case: Design collaboration
- Implementation: Virtual prototypes
- Results: Reduced costs, workflow synergy
Volvo Cars is renowned for its world-class safety systems and its commitment to quality engineering. In order to orchestrate the activity of its specialized teams, Volvo’s Virtual Experiences division created digital versions of vehicles and their subsystems that soon found surprising use cases during design collaboration, prototyping, and behavior validation.
To create photorealistic models of their vehicles, the team imported existing CAD data used in factory production into Unity’s real-time 3D platform using Pixyz Studio’s industry-leading tesselation and decimation algorithms. The resulting virtual prototypes provided a common language for interdisciplinary stakeholders to communicate updates and even validate user behaviors in fully interactive driving simulations. Volvo’s XR solution freed their engineers from a reliance on costly physical prototypes and improved the rate of iteration without compromising on quality. Downstream of that decision, the same 3D assets were instrumental to creating virtual customer experiences.


Innovator: Toyota Motor Corporation
- Use case: Design collaboration
- Implementation: AR simulation tool
- Results: Improved analysis, faster inspection
Toyota Motor Corporation tasked its XR development team to find a way to streamline the process of computational fluid dynamics (CFD) analysis. Previously an arduous task, CFD involves lengthy physical inspections of prototype vehicles to gather measurements for computer-aided analysis of their aerodynamics. Shortening this process could translate to faster go-to-market and potentially millions in additional revenue.
To actualize their brand’s commitment to kaizen, or “continuous improvement,” Toyota’s XR engineers decided to leverage Unity’s industry-leading data ingestion and intuitive 3D development framework in order to build advanced AR modules for Microsoft’s HoloLens 2 platform. The resulting mixed-reality overlays simplify CFD analysis with real-time airflow simulations, which ultimately reduces inspection turnaround from days to hours. As an added benefit to interdisciplinary teams, the 3D assets created for the project (which incorporated over 20,000 fully rendered vehicle parts) went on to inform the development of high-fidelity product configurators for the luxury Lexus product line and enhance design collaboration between engineers and product owners.
Industry closeup: Shipping and logistics

Innovator: Travancore Analytics
- Use case: Skills education
- Implementation: VR training module
- Results: Reduced costs, faster training
Forklifts are a key tool in last-mile shipping logistics, and operators must be trained in accordance with safety regulations to minimize the risk of personnel injury, accidents, or delays. That’s why Virtual Forklift partnered with Travancore Analytics, a firm dedicated to creating custom digital solutions. The team designed robust VR training modules for the HTC Vive that allowed trainees to operate forklifts and conduct procedural training lessons in a shared virtual space.
By providing a risk-free environment to learn and assess fundamental skills, Virtual Forklift reduced the likelihood of injury and damage in warehouse accidents, improved learner satisfaction, and cut the duration of on-site certification training by 75%.

Innovator: HR Wallingford
- Use case: Skills education
- Implementation: VR training module
- Results: Unburdened resources, improved training quality
In partnership with Harwich Haven Authority (HHA), HR Wallingford’s waterway experts used Unity’s real-time 3D modeling tech to create vessel bridge simulators that allow trainee ship pilots to navigate realistic waterway scenarios and encounter adverse weather conditions in a controlled environment.
With advanced wave dynamics simulations and scale replicas of real-world ports, bridge simulators at the UK Ship Simulation Centre also help harbormasters analyze shipping-lane traffic and evaluate new ships before they make their first call at HHA.

Industry closeup: Industrial manufacturing

Innovator: Bosch Rexroth
- Use case: Product education
- Implementation: Virtual showroom
- Results: Rapid GTM, improved sales conversions
Bosch Rexroth is one of the leading manufacturers of hydraulic drive and control technologies for industrial machines. Given the highly specialized nature of their products, static assets could only do so much to showcase product functions to prospective buyers. That’s why their XR development team decided to build a virtual showroom in Unity.
With the Pixyz Studio add-on, they could rapidly ingest dozens of complex CAD models and create dynamically tesselated meshes for fully explodable 3D models. This solution reduced the sales team’s reliance on physical demonstrations, permitting agents to conduct ad hoc virtual demos with just a VR headset rather than needing to invite prospective buyers on-site to view large machinery.


Innovator: Cross Compass
- Use case: Industrial simulation
- Implementation: AI Robotics Training
- Results: Faster iteration
Industrial robotics are trained to behave with meticulous precision and produce accurate results. As new advancements in artificial intelligence have made it possible to train self-correcting systems, Cross Compass needed to devise a safe way to introduce real-world variables into a factory floor environment in order to train its AI-powered industrial robotics.
Using Unity’s 3D development engine, Cross Compass virtualized the factory floor and industry-standard robots to run advanced simulations without risking damage to real-world equipment or personnel.
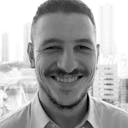
Industry closeup: Commercial transportation

Innovator: KLM Royal Dutch Airlines
- Use case: Skills education
- Implementation: VR training modules
- Results: Faster development, improved training quality
To ensure safe travels for 34 million passengers per year, the team at KLM’s XR Center of Excellence set out to produce immersive training environments that could familiarize pilots with every detail of the aircraft in KLM’s fleet. Using high-fidelity cameras, LiDAR depth scanners, and CAD data from a multinational aerospace manufacturer, KLM developers were able to quickly prototype true-to-life renders of every aircraft type in its fleet.
These impressive 3D models allowed the rapid development of immersive training scenarios that allowed pilots to interact with realistic control panels, familiarize themselves with new aircraft, and practice complex procedures within a virtual cockpit.


Innovator: Vancouver Airport Authority
- Use case: Operational efficiency
- Implementation: Digital twin
- Results: Enhanced insights, improved tasking
In order to create a unified data source for its various operations, the Vancouver Airport Authority created a completely digitized version of the airport and its surroundings that can be used by all teams. To capture data for exterior views, a helicopter outfitted with high-fidelity cameras and LiDAR detectors made an extensive survey of the airport.
This real-world imaging data was then ingested and rendered within Unity, enabling the creation of numerous visualization perspectives, including a CAD-derived interior view for optimizing gate layouts. Airport administrators use the exterior view to visualize real-time data for plane traffic and gate metrics, while the interior views permit staff to issue room-specific work orders throughout the airport.

Benefits of enterprise XR apps
In each developer profile, we’ve seen how a team targeted a business need and actualized the value of 3D data for vast organizational benefits. As you consider incorporating XR into your development pipeline, we recommend a few basic metrics for measuring potential ROI:
Reduced costs
Cost savings can be measured in a variety of ways, such as fewer accidents and injuries, a decreased reliance on physical prototypes, or simply a quicker development timeline thanks to simulated iteration phases. Other XR implementations (e.g., digital twins) may recoup expenses through improved insights, faster triage response, or a diminished travel cost for key personnel.
Unburdened resources
Virtual environments eliminate or diminish the need to source real equipment for every training lesson. Whether your staff specializes in medical devices, airplanes, or industrial robots, VR training allows them to hone skills and practice complex procedures in virtual environments, thereby freeing real equipment for use in the typical course of operations.
Increased safety
Virtual environments improve the quality of training by abstracting risk and maximizing student exposure to real-world scenarios before they encounter them on the job. This controlled, repeatable exposure to hazardous scenarios keeps individuals safe from harm and decreases a company’s overall injury liability.
Faster decision-making
Real-time 3D development captures the dual benefits of actual insight and future forecasting. Design-oriented XR implementations allow product teams to simulate real-world phenomena to test airflow dynamics or establish baseline tolerances for physical parts, while a monitoring app can render real-time iOT data as easily parsed 3D visualizations for optimization and triage.
Data liberation
Real-time 3D development frees CAD, BIM, and other 3D data formats from irksome access restrictions, seat licenses, and technical knowledge gaps by creating a common vector of communication between interdisciplinary teams. XR tools empower artists, engineers, and product teams to iterate and develop together.
How to approach XR apps
Industry-leading developers are unleashing the possibilities of XR with immersive solutions for training, collaboration, and industrial simulation. When deciding whether XR applications could benefit your organization, we recommend a few considerations and best practices:
Evaluate 3D data
Many organizations still lack a dedicated 3D design team. If you’re considering the value of XR applications for your use case, you should first decide whether your organization has a compelling user story that warrants upskilling your engineers or sourcing 3D developers. Take advantage of our online learning resources to see how Unity Industry fits within your workflow.
Address pain points
If your organization currently uses 3D data exclusively for manufacturing or production, there’s a good chance that its potential value hasn’t been fully realized. But before embarking on a project to free your 3D data, it’s important to determine its potential value relative to other considerations, such as:
- Who currently maintains 3D data within your organization?
- Who has access, and has access been limited for security or compliance?
- Does the data live in proprietary formats?
- Do stakeholders require an expensive license or technical acumen to use and manipulate those data?
These questions should provide a framework for determining whether an XR solution could benefit your organization.
Start small, aim high
Don’t try to boil the ocean. Start small, and ideate around ways that XR can address specific pain points within your organization. Even if you can already anticipate second-order use cases for an XR application, it’s better to adhere to design with a discrete MVP in mind.
The greater the fidelity of your assets – and the more care that goes into unlocking the value of your data – the better your chances of creating operational efficiencies within your organization.
Estimate ROI
Those interested in advocating for XR solutions within their organizations should estimate the potential ROI using the examples outlined throughout this document. Does virtualization correlate to explicit or implicit cost savings (e.g., decreased training duration, fewer prototypes, quicker development, less employee travel, or reduced liability)?
Though your solution should be developed around incremental progress, it’s worth reasoning out downstream benefits at this stage as well. Could accessible data visualizations be useful in marketing and sales materials or starring in an interactive customer experience at point of sale?
Choose platform-agnostic frameworks
To avoid trouble when hardware vendors update or modify their platforms, it’s important to design with a 3D development framework that simplifies the process of deploying to multiple platforms by avoiding vendor lock-in. When choosing a tech stack, be on the lookout for software solutions that allow you to create opinionated deployment configurations in various execution environments.
About Unity Industry
Unity Industry combines the Unity Editor’s real-time 3D toolkit and dynamic rendering pipelines with industry-leading data ingestion and ongoing Industry Success support to facilitate your digital transformation. The included Pixyz Plugin can parse over 70 file types, including CAD and BIM, with options for dynamic mesh tesselation and polygon decimation that make it easy to develop XR apps with 3D data.
Unity customers choose Unity Industry to save money, attain excellence, and improve the way interdisciplinary teams access 3D data.
Read the article
Fill out this form to get access to the latest customer success stories